Addressing integration and infrastructure readiness
Manufacturing organizations are embracing AI. While 76% are ready to adopt new technologies, only 34% see returns from AI initiatives.
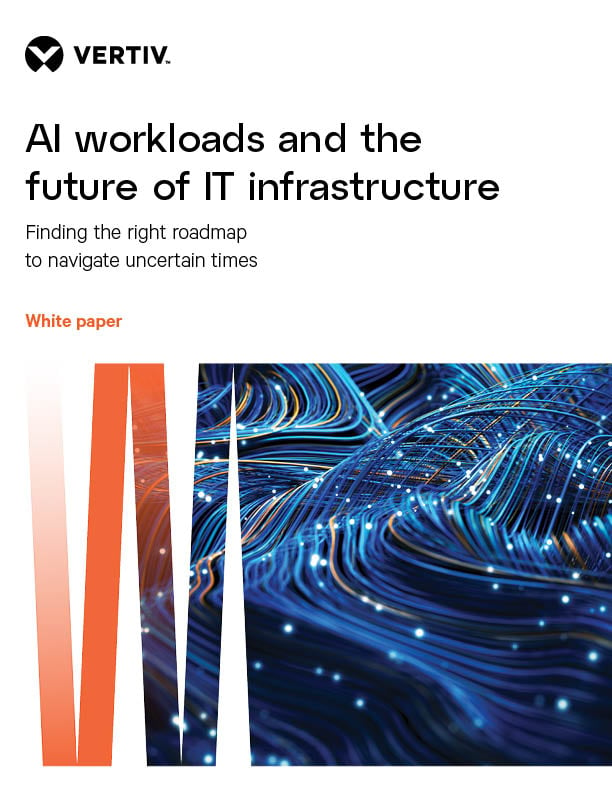
AI in manufacturing: Addressing integration and infrastructure readiness
The manufacturing sector is rapidly advancing its digital maturity, with 76% of firms ready to adopt new technologies and 34% already seeing returns from AI-driven initiatives, according to KPMG. This reflects a sector eager to leverage AI for smarter production, predictive maintenance, and streamlined operations. However, this optimism must be matched with practical solutions.
Manufacturers will need to continue to evolve their data center infrastructure, in order to meet evolving AI demands. According to the Manufacturing Leadership Council, 57% of companies are still piloting AI applications, carefully testing to identify the most effective use cases.
Are your manufacturing systems AI-ready?
The infrastructure to support AI-driven tasks such as predictive maintenance, that may utilize GPUS, could require advanced cooling solutions. At the same time, the explosion of data from sensors, machines, and supply chains calls for scalable data storage and secure management systems.
Many manufacturers are still catching up. According to the Boston Consulting Group (BCG), only 26% of companies have developed the capabilities to move beyond pilot projects and generate tangible value from AI. Additionally, a study by IFS North America identified limited skills and expertise, data complexity, and a lack of strategic direction as the top factors slowing AI adoption in manufacturing. These challenges highlight the gap between ambition and execution, even as the industry races to embrace AI’s transformative potential.
57%
are still piloting AI according to the manufacturing leadership council.
26%
have moved beyond pilot projects according to the Boston Consulting Group.
34%
are seeing returns from
AI-driven initiatives according to a KPMG Global Tech report.
AI imperatives in manufacturing
AI is no longer a futuristic concept for manufacturing—it’s a present-day imperative. Success will depend on not just investing in AI but also building the infrastructure to support it. As the industry moves forward, the race is on to bridge the gap between ambition and execution. Those who get it right will lead the next wave of industrial innovation.
Imperative | Use case examples | Data center requirement |
---|---|---|
Be transformative | AI-powered robotics and automation. | Cross-functional expertise. Holistic solution design. |
Be efficient | Predictive maintenance. Supply chain optimization. | Extend value and function of existing systems. Close-coupled systems that minimize space and energy requirements. |
Be first | Product development. Designs that reduce time and risk. | Pre-configured systems that reduce deployment times. |
Be confident | Quality control. Demand forecasting | Proven solutions supported by comprehensive services. |
Be future-ready | Autonomous manufacturing. Personalized production. Intelligent product design. Predictive quality assurance. | Interoperable, upgradable, and scalable solutions that can adapt to change. |
AI use cases in manufacturing
Companies are leveraging AI to optimize design, improve efficiency, and enhance quality control, transforming the factory floor with measurable results. For instance, General Motors has embraced generative design, using AI to create a seat bracket that is 40% lighter and 20% stronger, as highlighted in an Autodesk case study. Beyond design, AI-powered predictive maintenance is reducing equipment downtime by up to 50%, while machine learning algorithms optimize production schedules, boosting output by 20-30%, according to the World Economic Forum. Additionally, computer vision systems enhance quality control and detect defects with 90% accuracy, and collaborative robots (cobots) are improving worker safety and efficiency. These advancements are cutting costs, increasing precision, and enabling manufacturers to meet rising demand with greater agility.
Key takeaways:
AI delivers
real-world results
From cost savings to improved efficiency, AI is transforming manufacturing with measurable outcomes.
Infrastructure powers AI
Power management and edge computing are critical to support widespread AI adoption in manufacturing.
Strategic pilots lead to success
Identify high-impact AI use cases in manufacturing while building adaptable infrastructure for long-term growth.